What is Porosity in Welding: Crucial Tips for Getting Flawless Welds
Unwinding the Secret of Porosity in Welding: Tips for Minimizing Flaws and Optimizing Quality
In the detailed world of welding, porosity remains a consistent challenge that can considerably impact the quality and honesty of welded joints. Understanding the factors that add to porosity development is critical in the search of remarkable welds. By unraveling the mystery of porosity and implementing reliable techniques for problem minimization, welders can raise the standards of their work to accomplish exceptional top quality outcomes. As we dig into the midsts of porosity in welding, uncovering the tricks to its prevention and control will certainly be extremely important for specialists looking for to grasp the art of top notch weldments.
Comprehending Porosity in Welding
Porosity in welding, a typical concern come across by welders, refers to the visibility of gas pockets or voids in the bonded product, which can compromise the honesty and top quality of the weld. These gas pockets are usually entraped throughout the welding process as a result of different aspects such as incorrect shielding gas, polluted base materials, or incorrect welding specifications. The development of porosity can weaken the weld, making it prone to fracturing and rust, ultimately resulting in architectural failures.
By recognizing the significance of preserving appropriate gas securing, making certain the tidiness of base materials, and optimizing welding setups, welders can substantially lower the chance of porosity development. In general, a detailed understanding of porosity in welding is crucial for welders to create top notch and resilient welds.

Common Reasons of Porosity
When inspecting welding processes for possible quality concerns, understanding the typical reasons for porosity is important for preserving weld stability and preventing architectural failings. Porosity, characterized by the existence of tooth cavities or voids in the weld steel, can considerably jeopardize the mechanical residential or commercial properties of a bonded joint. One typical cause of porosity is incorrect protecting gas protection. Inadequate protecting gas flow rates or improper gas mixes can bring about atmospheric contamination, resulting in porosity formation.
In addition, welding at incorrect specifications, such as excessively high travel rates or currents, can create too much turbulence in the weld pool, capturing gases and causing porosity. By addressing these typical reasons via proper gas shielding, material preparation, and adherence to optimal welding specifications, welders can reduce porosity and boost the quality of their welds.
Methods for Porosity Avoidance
Implementing efficient preventive measures is critical in decreasing the incident of porosity in welding processes. One technique for porosity prevention is making certain proper cleansing of the base metal prior to welding. Pollutants such as read this post here oil, oil, corrosion, and paint can cause porosity, so thorough cleaning utilizing ideal solvents or mechanical methods is crucial.

Utilizing top quality filler products and protecting gases that are suitable for the base metal and welding process can dramatically decrease the danger of porosity. Additionally, keeping appropriate welding why not look here specifications, such as voltage, present, travel speed, and gas flow rate, is essential for porosity avoidance.
In addition, utilizing appropriate welding strategies, such as keeping a regular traveling speed, electrode angle, and arc length, can help stop porosity (What is Porosity). Appropriate training of welders to ensure they adhere to ideal practices and quality assurance procedures is also essential in lessening porosity problems in welding

Best Practices for Quality Welds
Making sure adherence to sector requirements and correct weld joint preparation are basic facets of attaining continually premium welds. Along with these fundamental steps, there are numerous ideal techniques that welders can carry out to even more boost the top quality of their welds. One secret technique is maintaining appropriate sanitation in the welding area. Pollutants such as oil, oil, rust, and paint can adversely affect the high quality of the weld, causing issues. Completely cleaning the work surface and surrounding location before welding can help reduce these problems.
One more best technique is to very carefully pick the ideal welding parameters for the details products being joined. This includes setting the right voltage, current, take a trip rate, and protecting gas circulation rate. Correct specification option ensures ideal weld penetration, blend, and general high quality. Using high-quality welding consumables, such as electrodes and filler steels, can you could check here significantly influence the final weld quality. Purchasing costs consumables can cause stronger, a lot more resilient welds with fewer flaws. By adhering to these finest practices, welders can continually generate high-quality welds that fulfill market standards and go beyond customer expectations.
Relevance of Porosity Control
Porosity control plays an important function in guaranteeing the stability and quality of welding joints. Porosity, defined by the existence of dental caries or gaps within the weld steel, can considerably jeopardize the mechanical residential properties and structural honesty of the weld. Too much porosity damages the weld, making it much more prone to fracturing, deterioration, and general failure under functional loads.
Efficient porosity control is important for keeping the preferred mechanical buildings, such as toughness, ductility, and strength, of the bonded joint. What is Porosity. By reducing porosity, welders can improve the overall top quality and integrity of the weld, making certain that it fulfills the performance demands of the intended application
In addition, porosity control is important for attaining the wanted visual appearance of the weld. Too much porosity not only compromises the weld but also detracts from its aesthetic appeal, which can be essential in industries where visual appeals are necessary. Correct porosity control methods, such as using the appropriate securing gas, controlling the welding parameters, and ensuring appropriate cleanliness of the base materials, are necessary for generating high-grade welds with marginal issues.
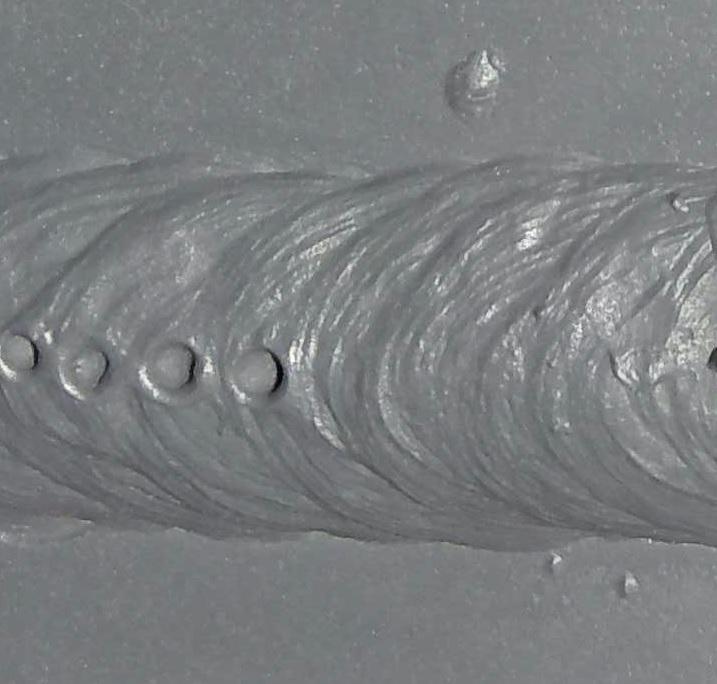
Verdict
In final thought, porosity in welding is a typical defect that can jeopardize the quality of the weld. It is crucial to control porosity in welding to make sure the honesty and toughness of the last item.